CARBURETOR REBUILDING PROCESS
Why rebuild a carburetor?
It is not always necessary to purchase a new carburetor in order to get excellent performance. Competition Carburetion has a detailed rebuilding process that includes a complete cleaning, inspection, machining, rebushing, recoloring and testing. These services are all available on a customer’s core or a used core from Competition Carburetion. Send in your core and we will give you an honest evaluation of the viability of the core and the cost to rebuild.
Please use the Competition Carburetion Set Up Sheet when sending in your carburetor.
Phase I Rebuilding
A Phase I rebuild will breathe new life into any carburetor.
-
The carburetor is disassembled and inspected. At this time, problems can be observed. All threads are checked.
-
The unit undergoes a two-step cleaning process. This begins with the spray wash cleaner and is followed up with an ultrasonic cleaning.
-
The clean carburetor is blown dry.
-
The main body and base plate are surfaced. The boosters are inspected for tightness and cracks. Air bleeds are sized per customer engine specifications. The power valve channel in the body is machined for clearance.
-
Base plate mounting holes are enlarged to give proper main body alignment during final assembly. The base plate receives a bushing set if needed. The proper butterflies are installed. Throttle shafts are checked for wide-open position.
-
The metering block is checked for straightness. The part is spot-faced and pressed flat if needed. The idle and emulsion bleeds are sized per customer engine specs. The power valve channel is also sized. Jets and power valves are selected then installed.
-
Float bowls receive the necessary float, needle & seat, and accelerator pump assembly.
-
Final assembly begins with the main body installation onto the base plate. All new screws are used.
-
The body and base are checked on the Flow Bench. The airflow through the venturi, as well as the signal draw on the main jet, is measured. Boosters are then moved into the best possible position.
-
Epoxy is added to the boosters for safety and stability. (This step is only completed if rules allow)
-
The metering block and float bowl are installed. All external adjustments are made.
-
The unit is set on the test motor for an engine check. On the motor, the carburetor is run to check idle and throttle response. After the test, the carburetor is drained of fuel.
-
After the engine test, lubricant is sprayed into the float bowl. All external screws are torqued to factory specs.
-
The unit is securely packaged for shipping.
Phase II Rebuilding
This service includes everything in Phase I plus:
-
The boosters are removed.
-
The venturis are machined to the maximum size allowed.
-
New boosters are selected and machined to match engine requirements.
Phase III Rebuilding
The phase I and phase II are both gauge legal. The phase III is not gauge legal. This process can only be used where there are no size restrictions.
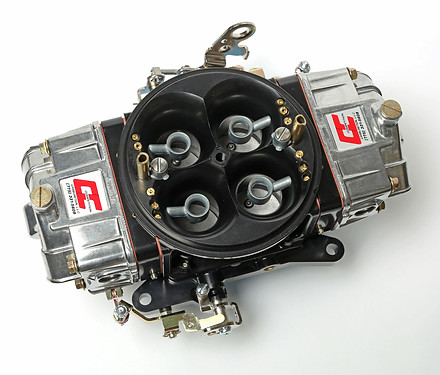
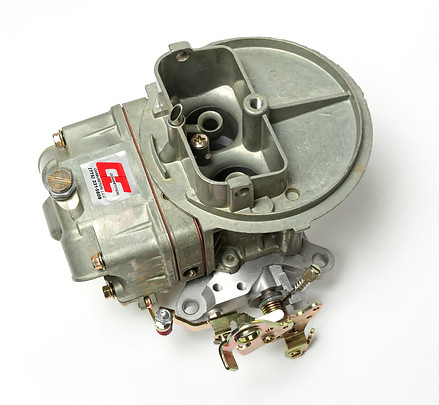
